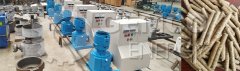

operating characteristic of pellet making machines
The utilization of biofuel mainly includes biomass gasification technology, biomass liquefaction technology, biogas technology, and also biomass solidifying technology. Among these technologies, biomass solidifying is recently widely accepted by the world, and biomass pellet making is most applied.
Biomass pellet making can be used for central boiler, thermal power plant, as well as civil heating and cooking. In European nations like UK, Swiss, Germany, France, Italy, Chili, etc. biomass pellets have become one of the most important fuels both domestically and industrially.
According to statistics, in 2005, the world consumes about 4.2 million metric tons of biomass pellets; in 2014, this figure rise up to 23 million metric tons; while it is estimated till 2024, there will be 50 million metric tons of consumption.
In the developing of biomass pellet production, flat die pellet making machine becomes one of the most popular pellet making machines because of its sturdiness, durability, good raw material adaptability, etc. It is the most suitable choice for home users and small workshop or small plant users.
Here we’d like to specify the pellet making technology of flat die pellet making machine for sale and its features.
Flat die pellet making machine composition and forming principle

Depending on the motion state of the components, flat die pellet making machines can be divided into roller rotating type (R-type pellet making machine) and die rotating type (D-type pellet making machine). D-type is usually used for softwood raw material and agricultural waste, while R-type is mainly for hardwood raw material.
Roller rotating pellet making machine working principle:
The electric motor drives the main shaft by the function of reduction gearbox, and the main shaft drives the roller. Together with its rotation horizontally, roller itself also turns vertically around the roller shaft. While making pellets, the biomass raw material is fed into the feeding chamber. Under the combined action of rotating roller and material scraper, the biomass raw material is evenly spread on the flat die. Over the driving of main shaft, roller rolls on the raw material in rounds and presses it into pellet machine die holes. Then the biomass raw material is shaped and kept in the die holes. Gradually, cylindrical pellets are extruded out from the flat die, then cutting knife cut them into regular length, and the pellet scraper push the pellets out from the pellet making machine.Why pellet making machine for sale can make solid biofuel?
Biomass raw materials are mainly from plants, and plants contain cellulose and lignin. Under the action of gravity, raw material clings to the flat die. When roller goes forward, the raw material is pressed, so its molecules continue to go into the interspaces of other molecules, and the air inside such interspaces is discharged. Gradually, the densely pressed raw material enters the forming area (where the die hole has certain tilt angle). In this area, the pressure continues to increase, molecules distort and plastically flow. The great friction between roller and raw material will generate great heat, and the great heat will cause the lignin to soften and have good adherence. Then the softened lignin will combine with the cellulose. After going through the shaping and shape keeping areas of die hole, solid biomass pellets are formed.
It may be a little complex for non-experts, but don’t worry, you only need to know that pellet making machines can make good pellets fuel from waste biomass, and that’s enough. (Learn about how to choose pellet making machine.)
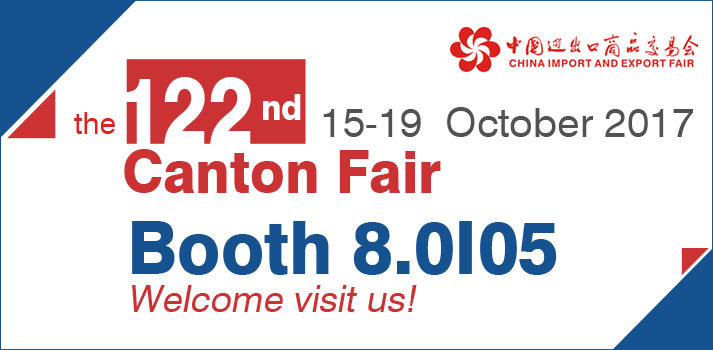
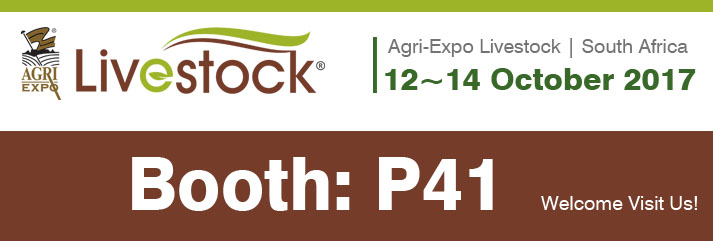
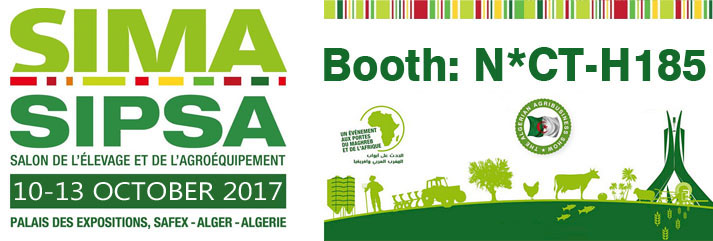